Making Tires in the Age of Advanced Automation
With the rise of AI, more advanced robots, and the need to tightly control inventory, how has Kumho Tire evolved its tire manufacturing process?
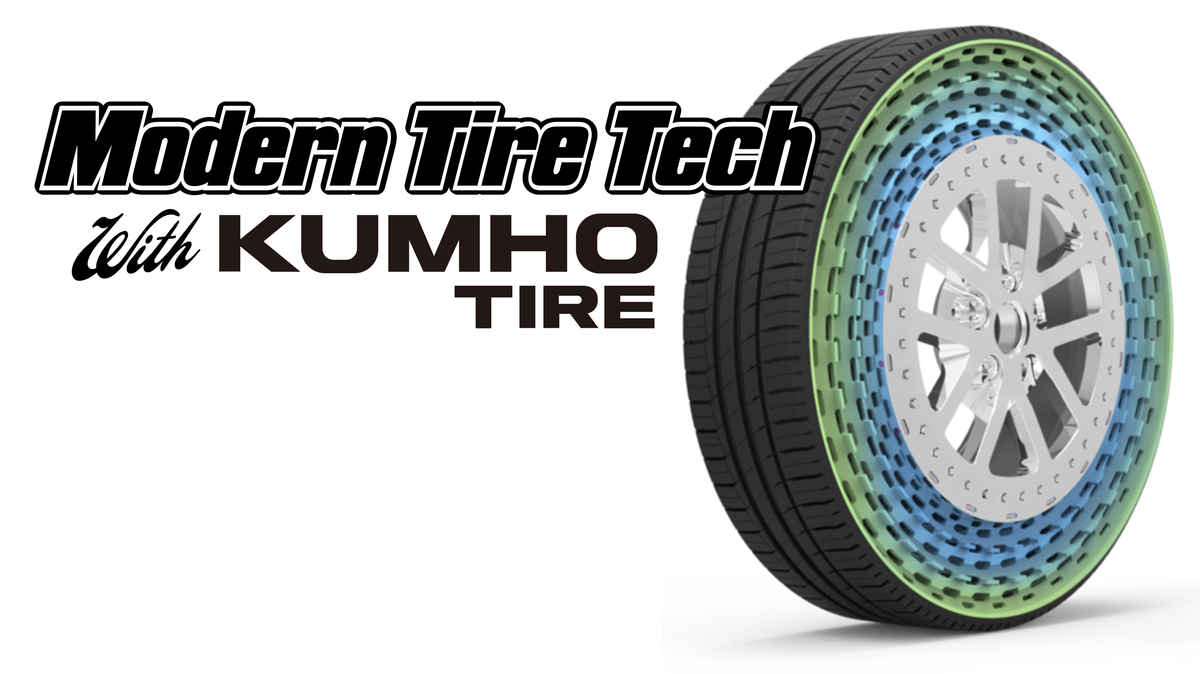
With the rise of AI, more advanced robots, and the need to tightly control inventory, how has Kumho Tire evolved its tire manufacturing process?
When it comes to manufacturing a tire, it’s no longer just a process of creating a mold and compound and just simply hoping for the best or trying repeatedly until it’s right. What used to take years of research and development has now been reduced to just a few months. Where you needed to build a physical prototype or development tire can now be modeled accurately by a computer and iterations changed on the fly before even making the mold. Essentially, when you see the physical tire at a show like SEMA, that tire has already seen virtual years of development. But that’s not all that has changed when producing a tire at Kumho Tire.
Note: Some links may lead to Amazon pages where I do make a commission if you decide to purchase items from those links.
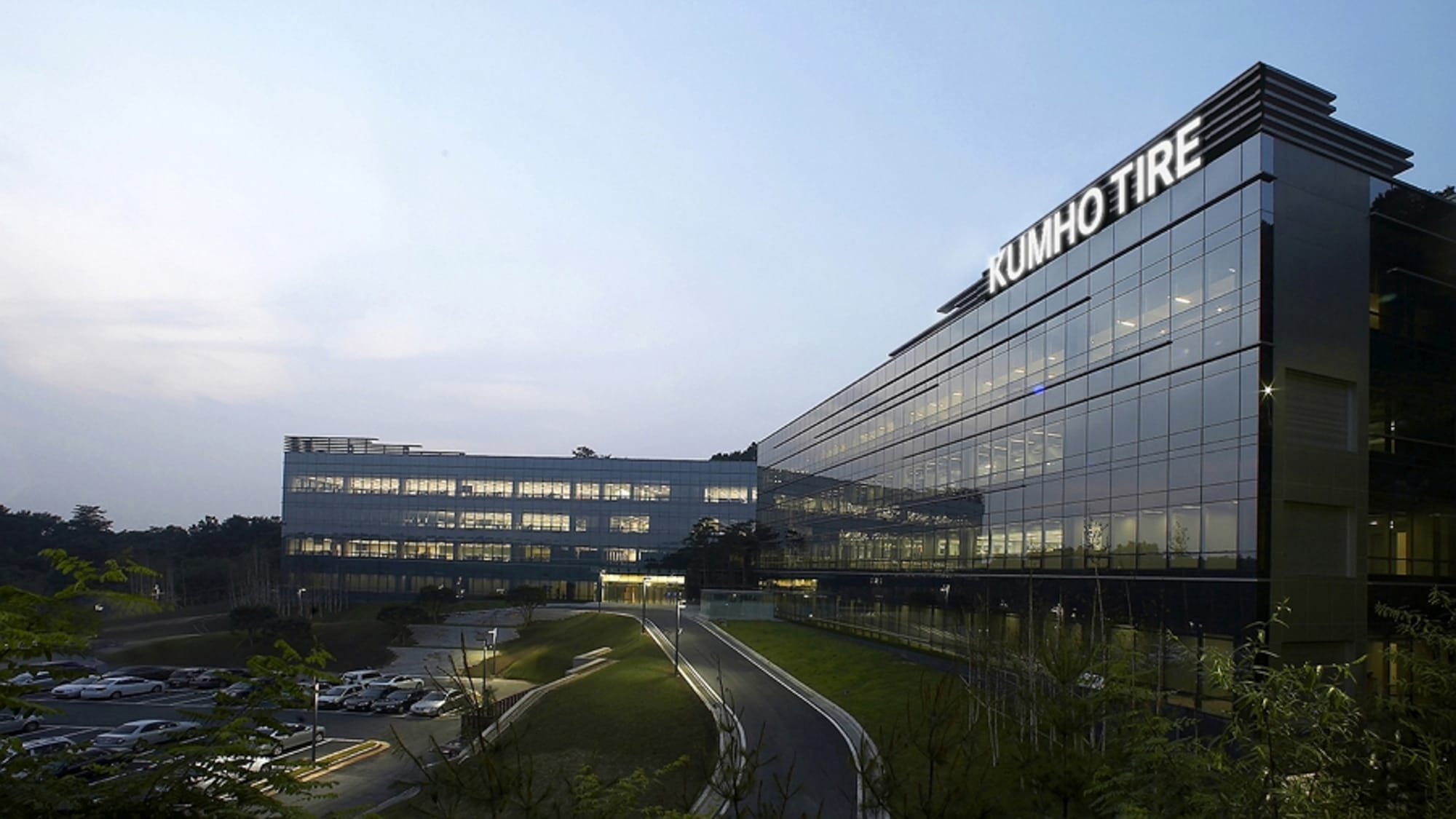
When I was introduced to the Kumho Tire Ecsta and Road Venture RT, one thing was rather clear: tire technology has changed since the last time I even looked into it about five to ten years ago. Development time has sped up thanks to new computer models that not only test the ability of tread patterns, but even the way compounds work in real life can be created virtually. Now, with Artificial Intelligence being used for everything nowadays, Kumho Tire expects both their development time and materials costs to reduce significantly. When I asked the Korean tire brand about how the process of making tires has changed it directed me to speak to Rick Cunat, managing director at Kumho Tire USA’s technical center in Akron, Ohio.
The Digital Twin: A Virtual Tire for Testing
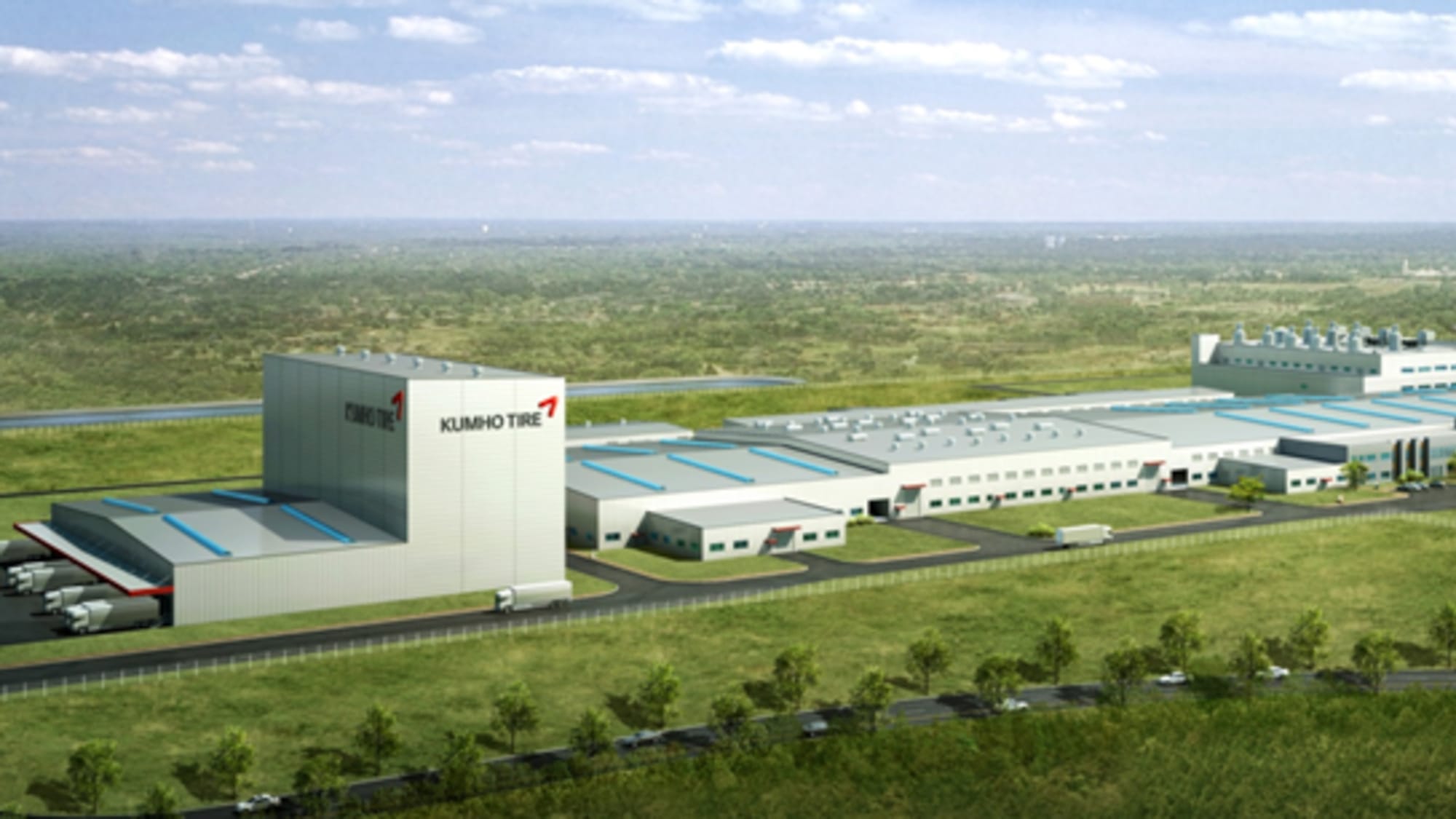
It’s good to start with the conception of a tire first, as that’s where much of the focus has changed in its development at Kumho. It calls this digital copy the “Virtual Twin” and this computer-generated tire sees the same testing as a physical tire would, just not in the real world. This alone accounts for much of the time and cost reduction mentioned above, but there is a new player in this game: Artificial Intelligence, or AI.
In this case, AI isn’t being used in writing out press releases or creating silly images of impossible tires for social entertainment. Instead, it’s being used in more useful ways that have real world use. The first is digesting research of materials into meaningful, but condensed language for researchers to help choose a potential compound or tire design that will work in real life. Soon, Kumho sees its AI working on tire tread patterns for the virtual twin tires to find the right design that offers the least compromises or the best performance for the goals it sets out for things like wet grip, noise reduction, and more. “In the future, we plan to build a platform to derive new insights through data-driven decision-making for design direction and research data analysis,” said Cunat, “In addition, we plan to shorten tire design time and enhance development efficiency through the development of various AI technologies in the product development process or tire Generative Pre-trained Transformer (GPT).”
Rapid Prototyping with 3D Printing
Another technology that has seen dramatic rise in all forms of industry is 3D printing. While the process itself is rather old, the rapid scaling of capabilities has changed how everyone–even readers like yourself–have been able to make things out of many types of materials from resin to metals and beyond. For Kumho, 3D printing has allowed easier and less expensive prototyping methods for mock-ups on tread patterns and sidewall designs. While a virtual twin will give you valid data, looking at something in real light will help you decide if a design is pleasing to the eye at all angles. It also allows Kumho to test out technologies like the internal spokes for airless tires and how 3D printing might be a direction towards real world production, but Cunat told me that for mass-scale production, “there is no plan, yet.”
Changes to Tire Manufacturing
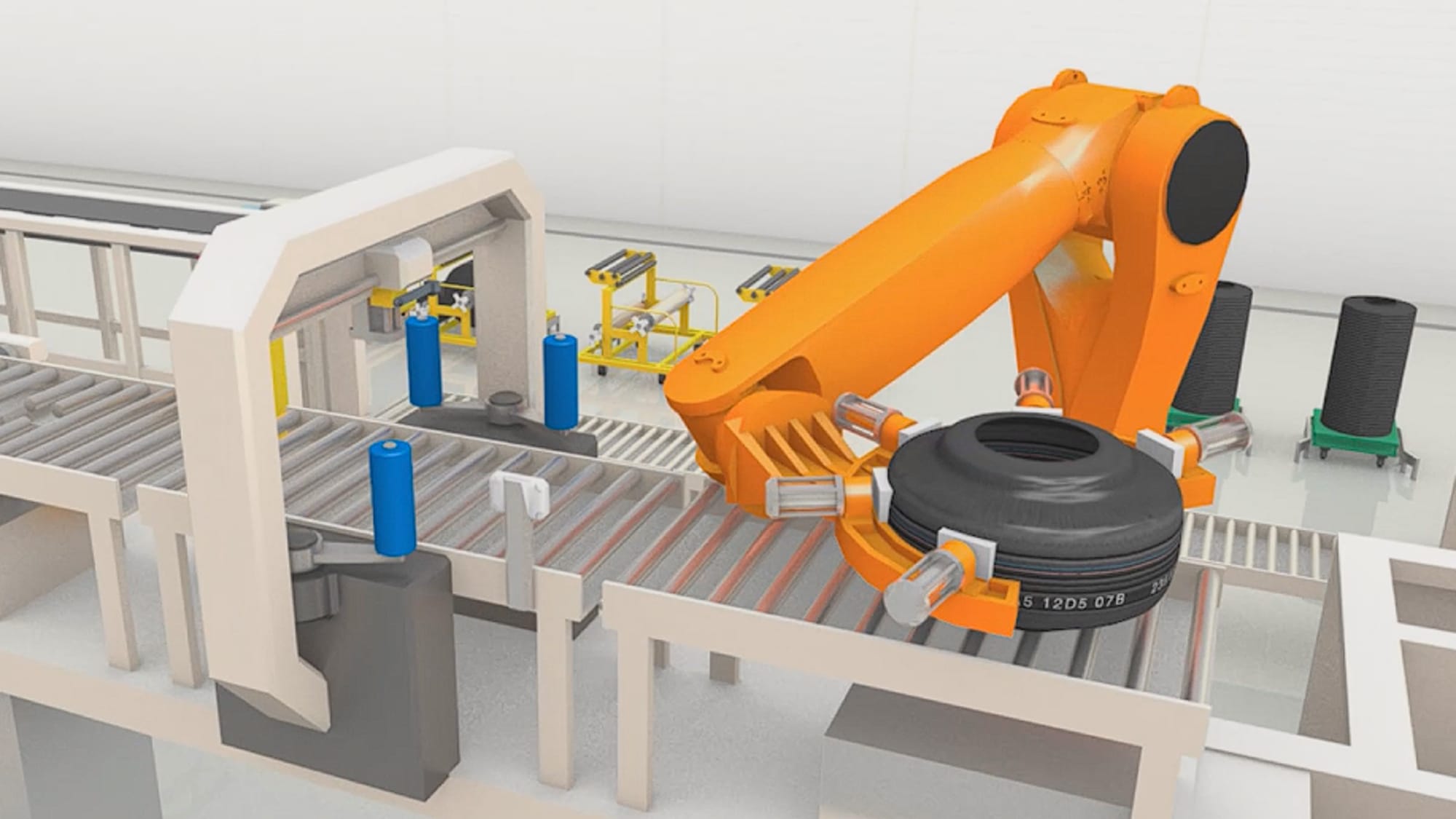
Once a tire has been developed, validated, and approved for manufacturing, more changes to process for Kumho continues. The process of making a tire for consumer use has changed thanks to automation and tracking controls. Raw materials storage and use was once a fully manual process with paper tags and is now tracked using RFID and automated storage and retrieval systems. Mixing compound materials, reeling that material, and even inspecting it is all done by automation. Loading and transporting these raw materials and new Kumho tires are also automated to ensure that every step is precise, repeatable, and as efficient as possible.
Even the raw materials have seen dramatic changes from the past five to ten years as eco-friendly tires have become the demand by all customers of Kumho tires. It’s not just the end product that customers are worried about, it is the entire process of making a tire. “Kumho Tire takes the environmental issues arising from the production, usage, disposal of tires seriously, establishing a circular economy system from product design to disposal,” its media representative told me. To make its tires more sustainable, 80 percent of a tire is made from recycled black carbon materials like recycled PET plastics, steel cord, and synthetic rubber. Silica–that’s mixed into the rubber compound and aids in all-weather traction–is obtained from natural resources like burnt rice husks while resin is extracted from pine tree sap. Even the oils needed to make a tire is sourced from sunflowers. That, however, only makes up 25.7 percent of the sustainable raw materials Kumho Tire uses. In five years, Kumho expects that percentage to rise to 40 percent and to be fully using 100 percent sustainable materials by 2045. “In realizing these goals, Kumho Tire aims to provide not just products but the value of a sustainable mobility experience,” said Kumho’s media representative.
Heavier Vehicles are in Our Future
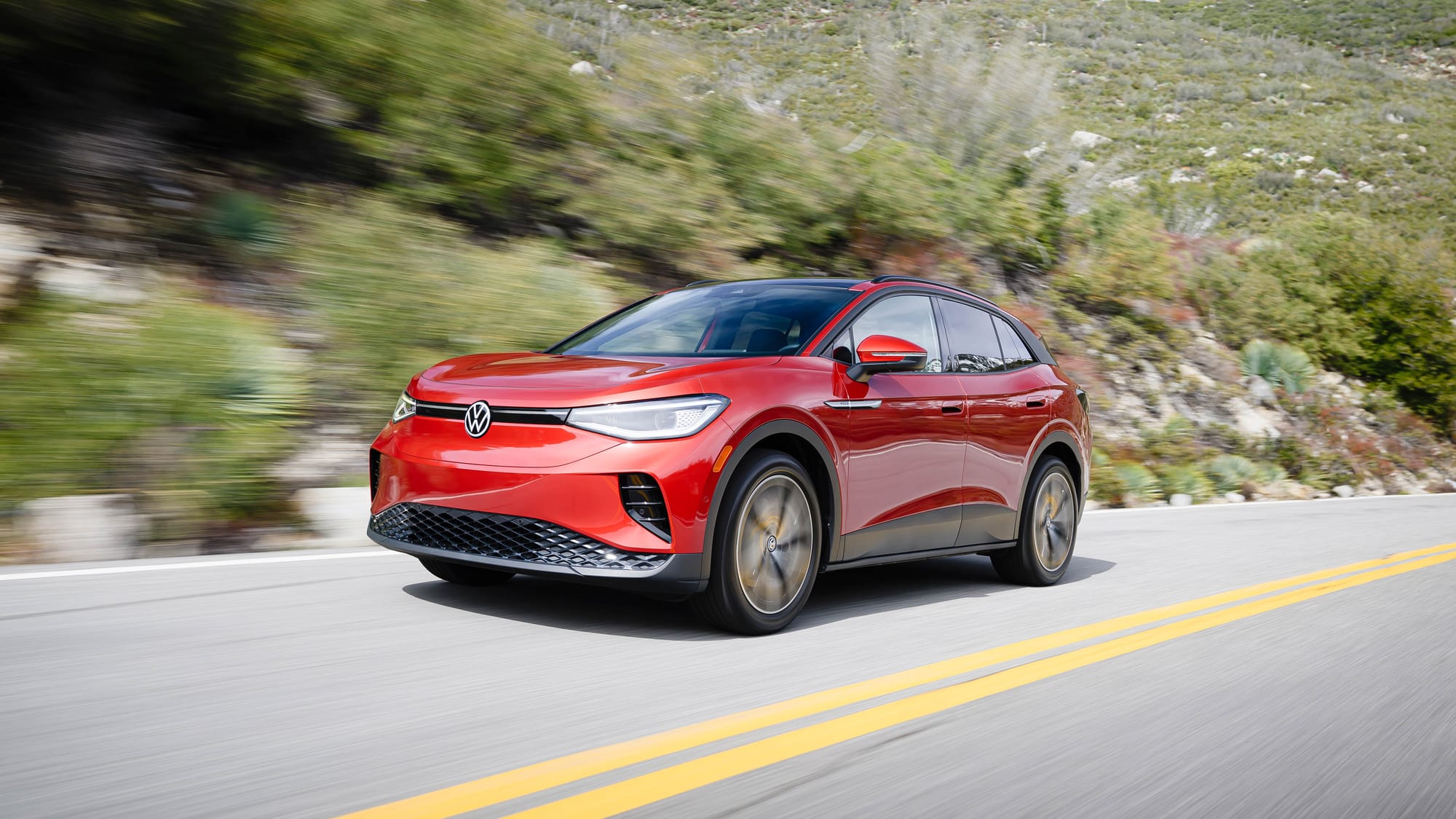
Looking at where we are and where most vehicles on the road will feature some sort of electrification in the future, vehicles will continue to increase in weight. Kumho, for its part, is already well past the development phase for tires for these vehicles. Back around 2021, Kumho was already developing tires for the first true generations of mass production electric vehicles (EVs) like the Nissan Leaf and are already leveraging this developmental experience on vehicles like Extended Range EVs (EREVs) as well as higher battery capacity, long range electric vehicles.
Its newest tires will feature compounds that not only allow for 80,000 miles of use but also retain a low glass transition temperature (also known as Tg). This is the temperature at which the rubber goes from a glass-like state to its rubbery state. There are also new belt technologies that allow the use of mono-wire in the steel belts over stranded wire that help reduce the weight of the tire, allowing for equal performance with better efficiency and capabilities.
The Future of Tires is Airless, but Not Right Now
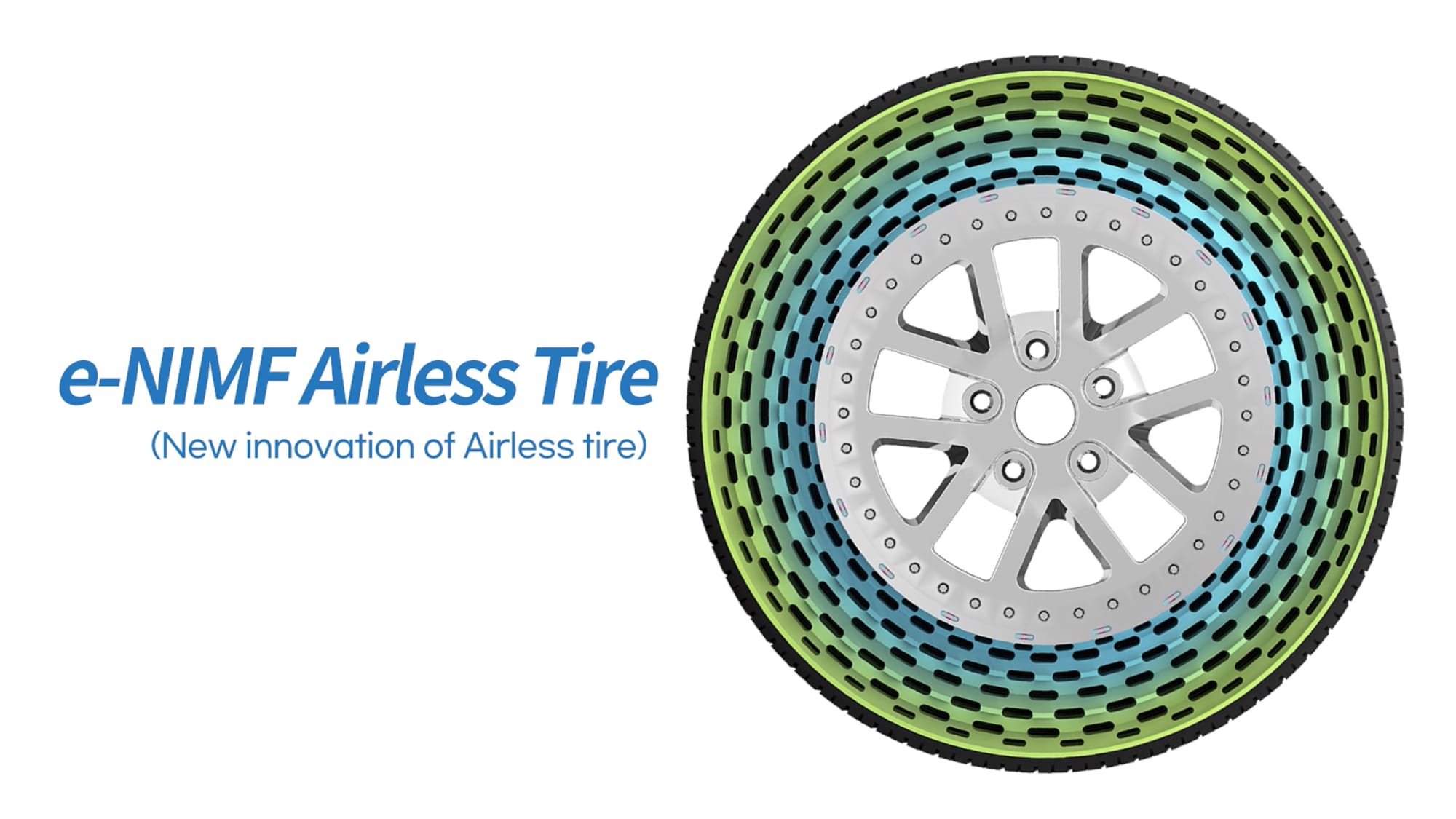
Future tire talk will always involve the idea of airless tires. It’s a good reason: most tire failures and reduced mileage for both internal combustion engine vehicles and EVs are tires with low air pressure. It’s been a development for decades in the making with no manufacturer really breaking through to the road-going environment. At the moment, these tires are limited to low-speed vehicles like micro-mobility, delivery robots, landscaping, and heavy industry vehicles. Kumho has airless tires and–as mentioned before–they are using 3D printing to help develop the technology now but focused on the smaller vehicle uses like unmanned autonomous and robotic vehicles. But they aren’t giving up on transitioning to the cars, trucks, and SUVs we all drive daily. “We are currently focusing on low-speed airless tire technology and are aiming to develop high-speed airless tire technology for passenger cars in the near future,” said Cunat, “For example, we will develop airless tire technology that can achieve performance similar to pneumatic tires by improving the tread band technology obtained from the development of low-speed airless tires and developing new spoke technology.”
For the time being, tire technology will look the same to someone who only views their tires are part of a machine that simply takes them from point A to point B. Nothing radical will be on the horizon in the very near future. But for those of us who look deeper, tires are developing at a rapid pace with interesting evolutions in both development and manufacturing. It’s not just an interesting time for Kumho Tire, it’s an amazing time for every part of the automotive industry. It’s just that tires will continue to be the biggest players in how our vehicles will perform.
Before You Go
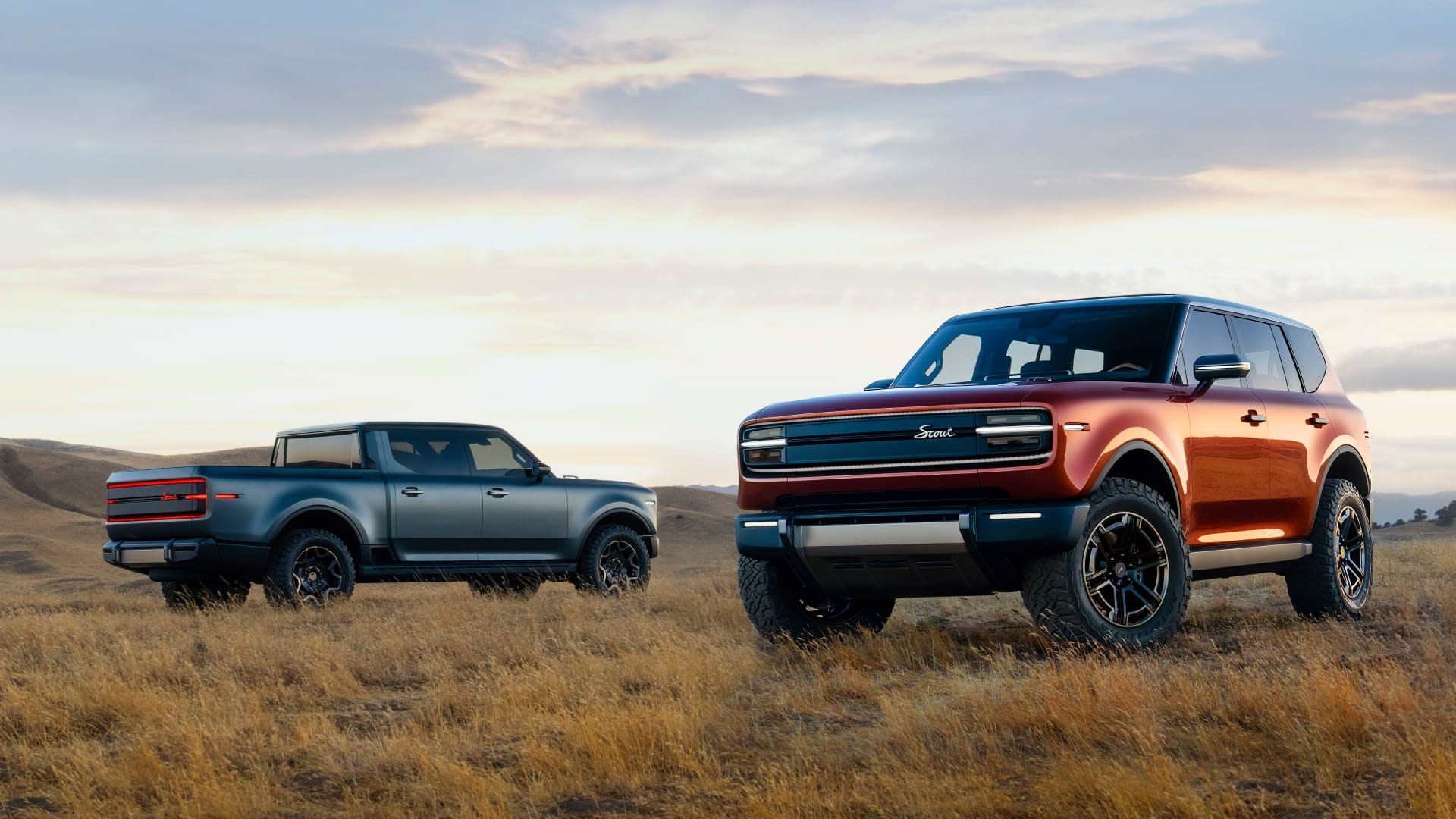
I want to encourage you to support me on Patreon. Carbage is going to be hitting it hard this year and I need your help to bring you awesome coverage and content all year long. All you need to do to support Carbage is donate as little as $1 per month. That little amount makes a dramatic difference when more people support the site. You can also sign up to receive more stories on the site to know when they go live, comment, and get exclusive access to our Discord and other unique features to help me create more stories and videos like this and more.
Comments ()