Feeding the Fire: The Parts of a Basic Electronic Fuel Injection (EFI) System
The modern Internal Combustion Engine (ICE) found on nearly all cars, trucks, and SUVs today are fed by EFI. Here’s how that fuel system works.
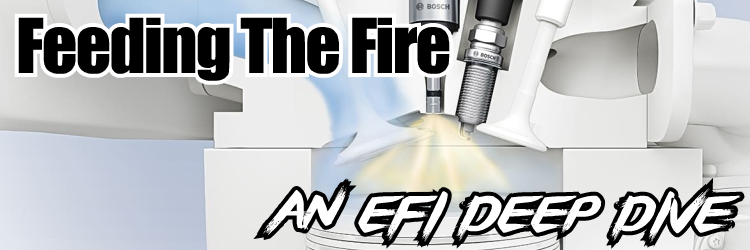
The modern Internal Combustion Engine (ICE) found on nearly all cars, trucks, and SUVs today are fed by EFI. Here’s how that fuel system works.
EFI, electronic fuel injection. It’s an acronym that’s not discussed much outside the automotive enthusiast space because every modern car since the 1980s has had it while trucks and SUVs have had it in the early 1990s. It’s so common today that any other type of fuel injection system is just something unknown to the average car buyer, new or used. While the way fuel has been injected into the cylinders has changed, most of the fuel injection systems are essentially the same between direct and multiport injected systems. I’ll discuss those similarities and differences in this story on your EFI system.
Before We Go Further
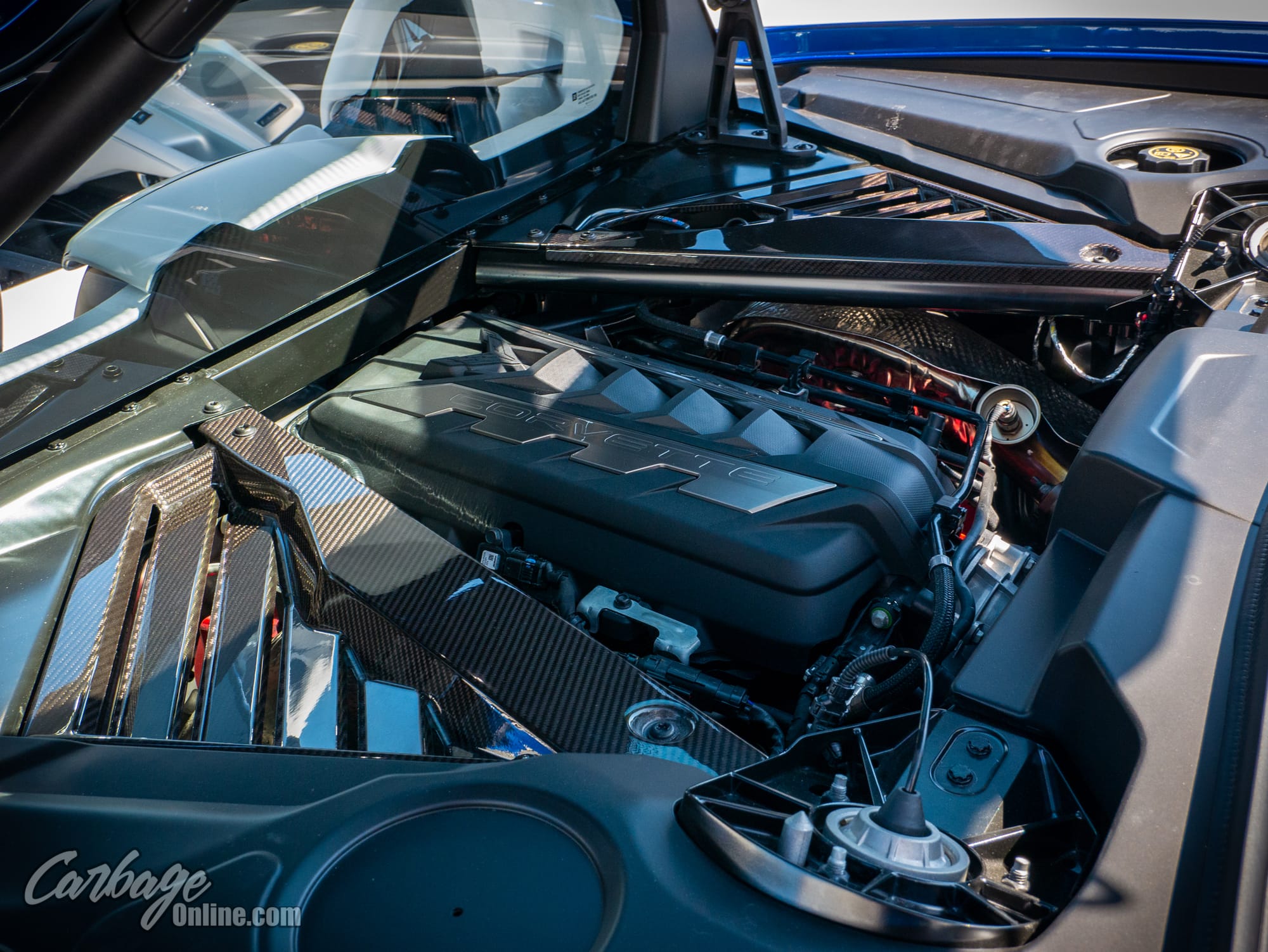
I want to encourage you to support me on Patreon. Carbage is going to be hitting it hard this year and I need your help to
bring you awesome coverage and content all year long. All you need to do to support Carbage is donate as little as $1 per month. That little amount makes a dramatic difference when more people support the site. Now that’s out of the way, let’s get on with this story on how electronic fuel injection systems work.
Fuel System
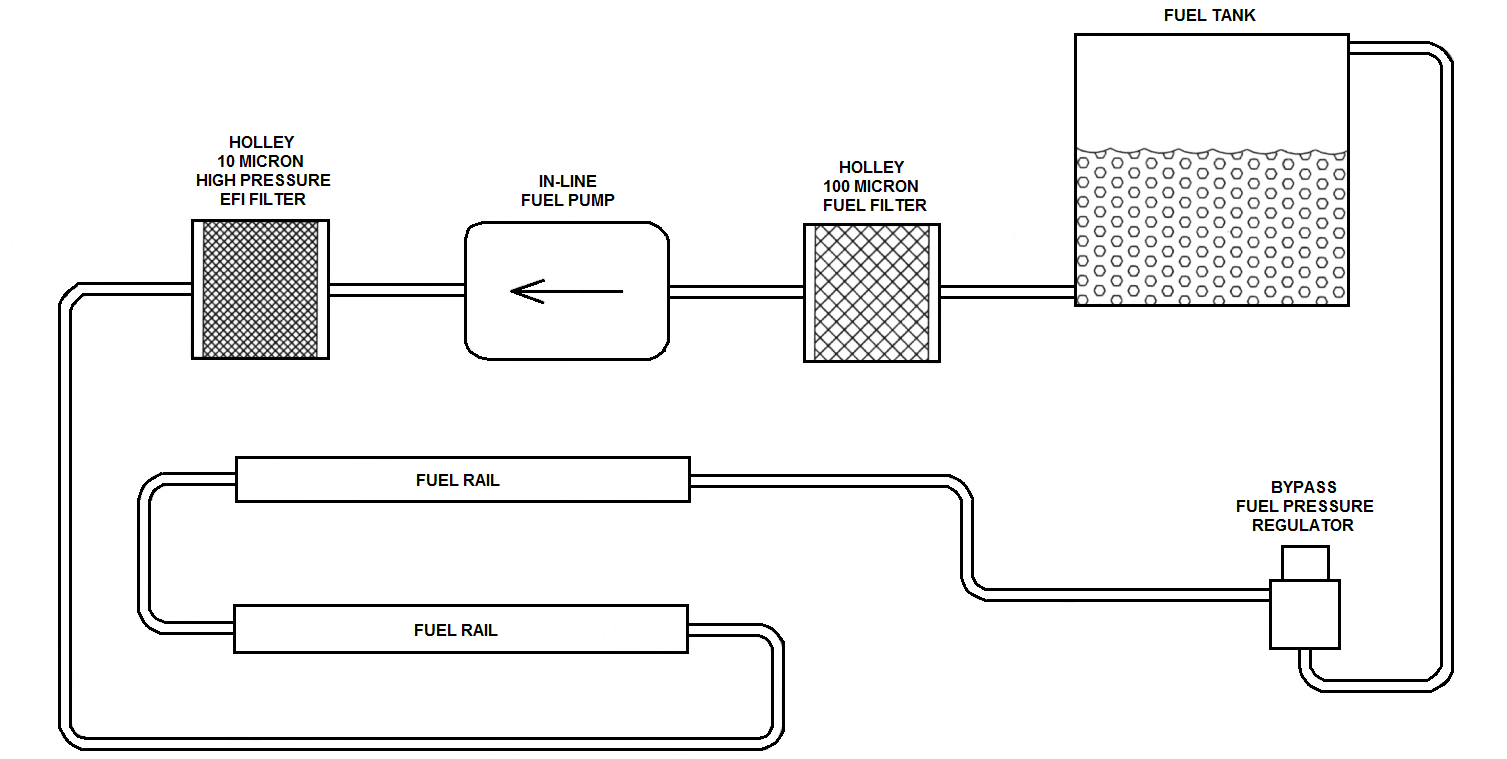
Most people like to compare their car to the human body. It’s not a bad comparison but it can get some people confused. Especially when you say that the oil is the “lifeblood” of the engine when it doesn’t serve to carry any energy like fuel does. Oil lubricates the engine while fuel, when mixed with air and ignites, creates power and torque. What we’ll be discussing is the now common electronic fuel injection (EFI) system. I’ll discuss carburetor, diesel, and throttle body injection (TBI) fuel systems in more detail in future articles.
Fuel Pump
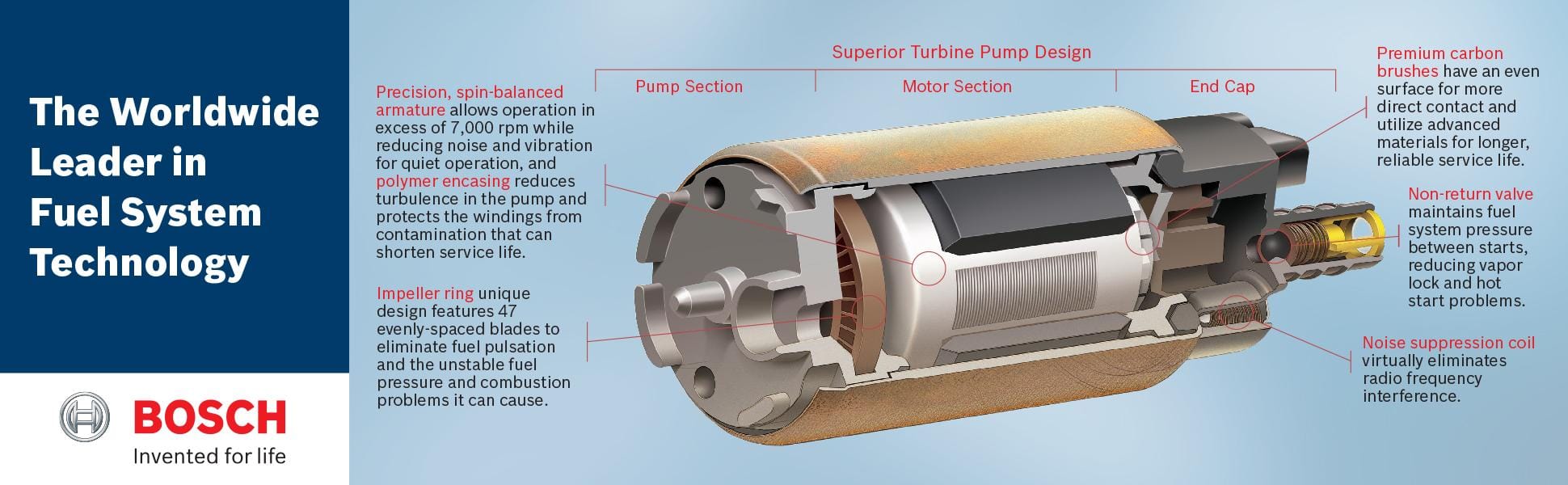
The modern EFI pump uses an impeller to pull fuel from the fuel tank. Its shape is very similar to the impeller of a jet engine or in an automatic transmission torque converter. Its operation, however, is very similar to how the vanes of a vented brake disc work. The design is a radial fan type, where—in the simplest terms—the blades create a low-pressure area on the outside of the impeller as it rotates. The high-pressure area between the blades flows in to fill in that low pressure area, which then creates a low-pressure area behind that to pull in more fuel.
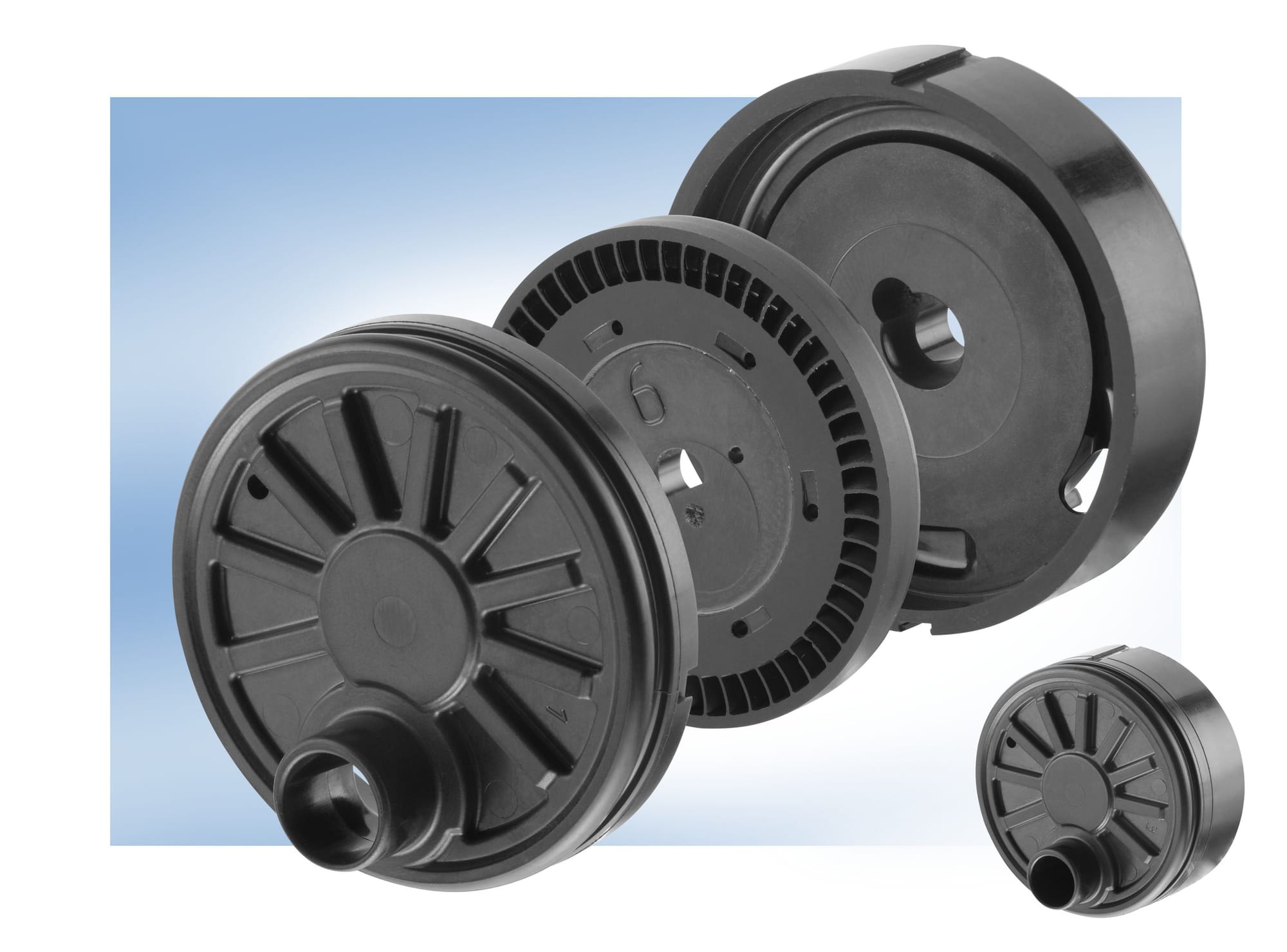
This creates a quiet system over a gerotor type pump but with more pressure than a screw type pump. It is a delicate design and if a vane is broken, the pump will fail. There is an initial filter on the fuel pump that’s commonly referred as the “sock filter.” This is the first line of protection from debris and particles that could be in the fuel. It does not filter the fuel from micron-sized particles like your fuel filter does.
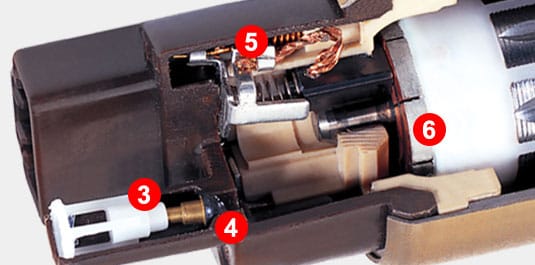
Most of the fuel pump body is the electric motor that drives the impeller. Fuel flows around the armature as it spins around to not only lubricate the pump but also keeps it cool. The outlet of the pump features a one-way check valve (number three on that Denso image). There is also an over-pressure relief valve to allow fuel to pour back into the tank if there is too much pressure at the outlet (number four on that same image).
Fuel Filter
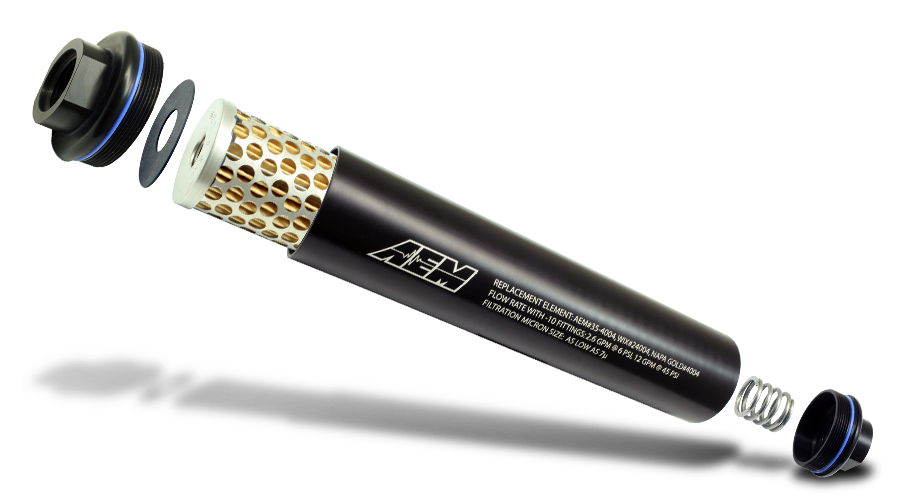
This is the next line of defense against debris for the fuel system and is usually closer to the engine, but not always. The filter is usually rather simple with a paper medium to block debris that can be introduced in the fuel lines to that point. It can also catch many deposits from fuel that the sock filter misses as it’s designed to catch micron-sized particles. It also catches the carbon debris left by the brushes of the fuel pump motor. While you can find filters that attach to the line, most modern engines have their fuel filters inside the housing of the fuel pump. They can be replaced, but with some difficulty for the average home mechanic.
The Modern Take: Direct Injection VS Multiport Injection
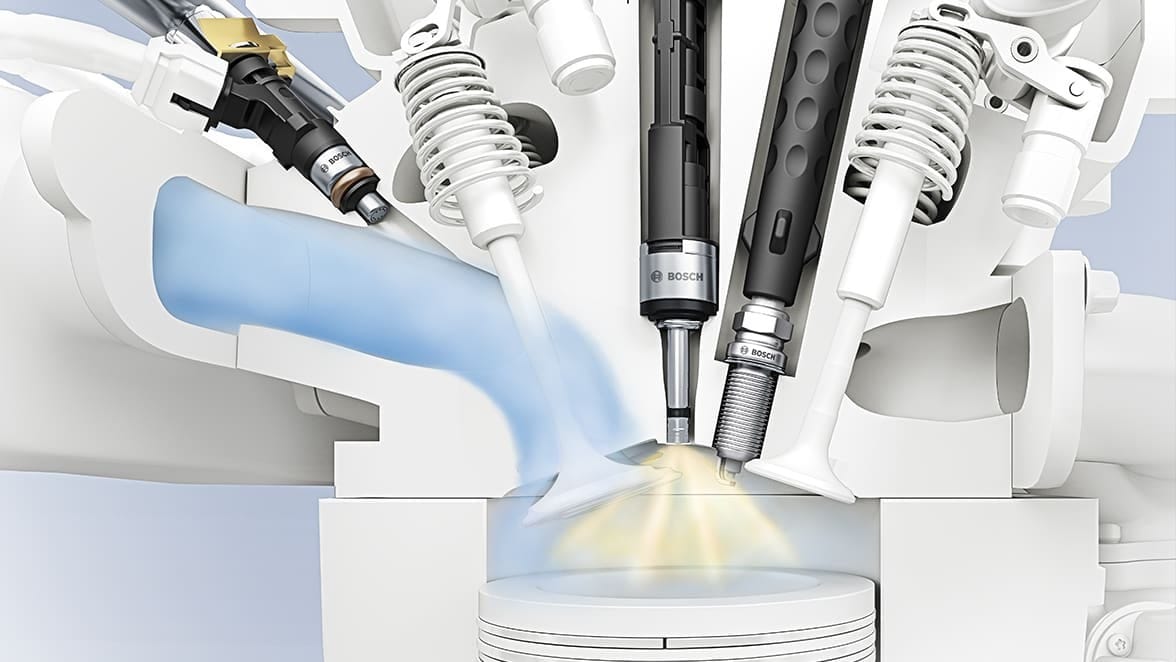
Here is where things start to diverge between multiport injection and direct injection systems. Prior to the mid-2000s to early-2010s, most vehicles were fed fuel by multiport injection. This system delivered fuel to the combustion chambers via injectors on the intake ports. Past that point and you start to hear about direct injection and the difference is more than the name. This system injects fuel directly into the engine cylinder though the head in what is known as the “combustion chamber.” This leads to better efficiency of an ICE, easier startup (especially for start-stop operation), and better tailpipe emissions.
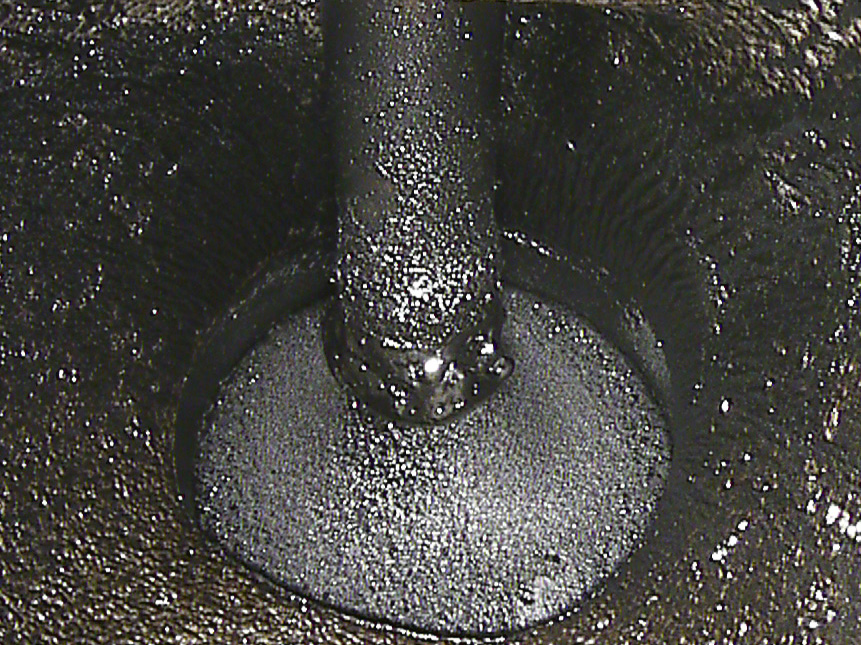
It comes at a cost of higher carbon build up on the backside of the intake valves as multiport fuel injection helps keep them clean and lubricated enough to allow the force of the valve closing to break off that carbon. This can also lead to pre-combustion—or “ping,” an event that ignites the fuel before the compression stage of the four-stroke cycle—that can lead to many other issues including engine failure. That’s why you’ll see some engines utilize a system that combines the two, injecting via the port-mounted injectors to help with that carbon build up. The only other option is to media blast—like sandblasting but without the cabinet—the intake valves to remove the carbon, a time-consuming and expensive maintenance procedure as you need to remove the intake manifold to access them and have the special equipment required for the blasting service.
Fuel Pump Relay or A Fuel Pump Control Unit
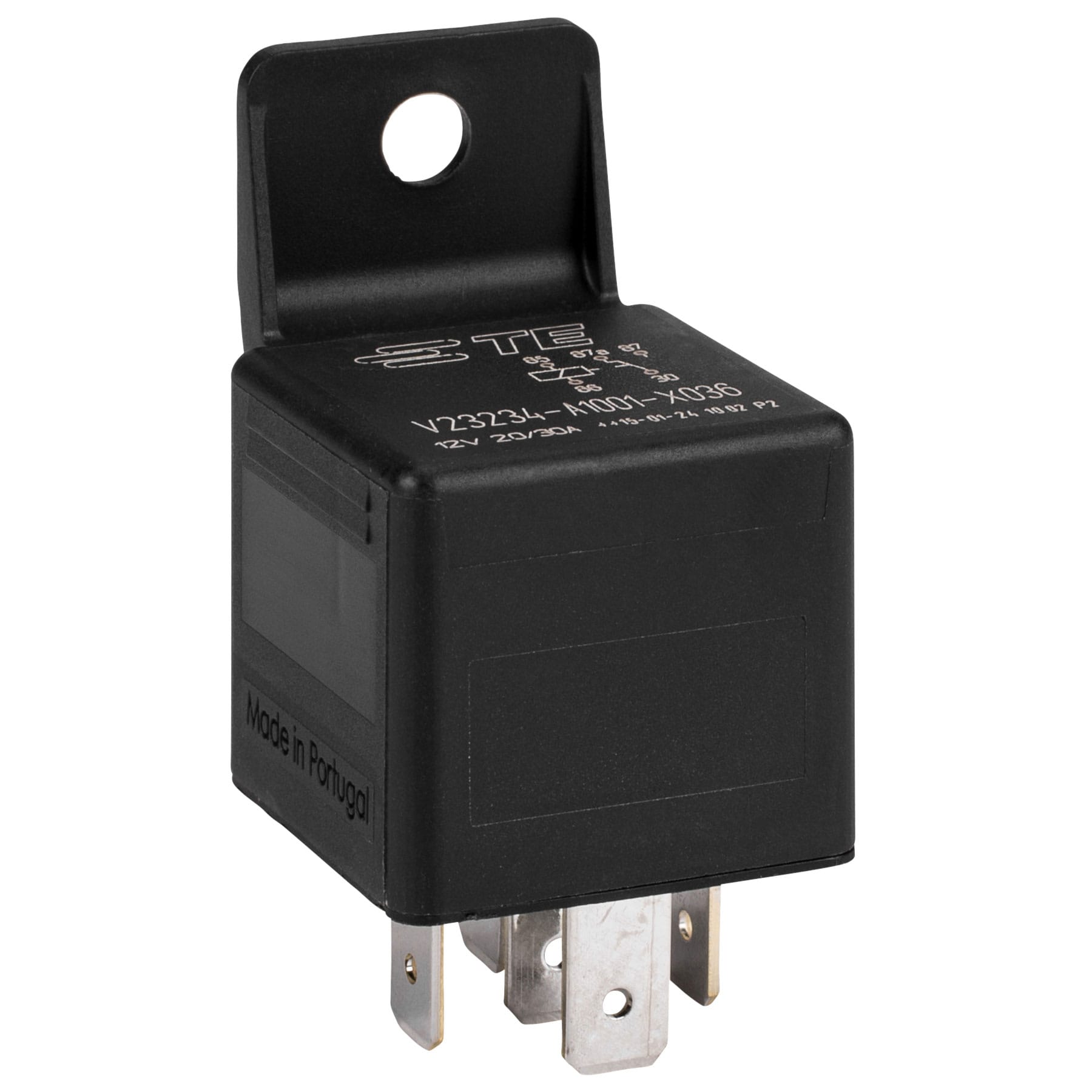
The fuel pump relay is basic and just like every relay in your vehicle. It takes a low voltage and current signal from the powertrain control module (PCM) to switch on a higher voltage and current signal directed to your fuel pump. Your PCM can’t handle the high 12-volt and current required by your fuel pump as it’s designed for 3.3- to 5-volt signals. If your PCM did get that same 12-volt signal, it would “burn out,” sometimes very literally. That’s why it must use a relay instead, at least in older vehicles.
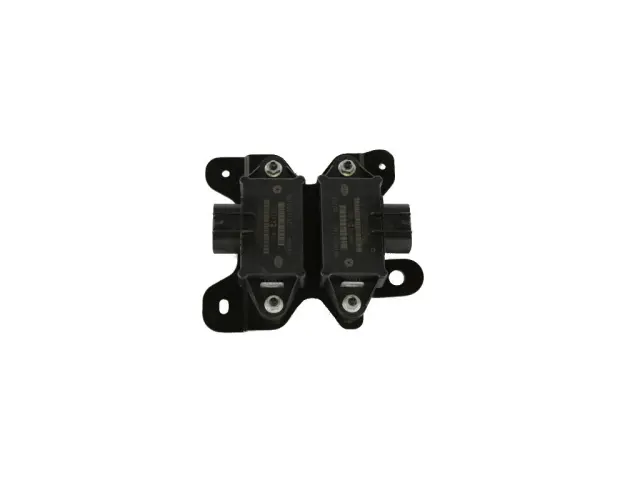
Modern cars, trucks, and SUVs utilize a fuel pump control unit—or module, depending on the manufacturer—that takes the place of the fuel pump relay. It still works the same in a basic sense in handing off higher voltage control away from the PCM, but it introduces precise control over the fuel pump via pulse width modulation (PWM) that a relay just can’t do. The reason is due to electromagnetic saturation and we’ll cover that issue next with the fuel injector.
Fuel Rail and Injectors
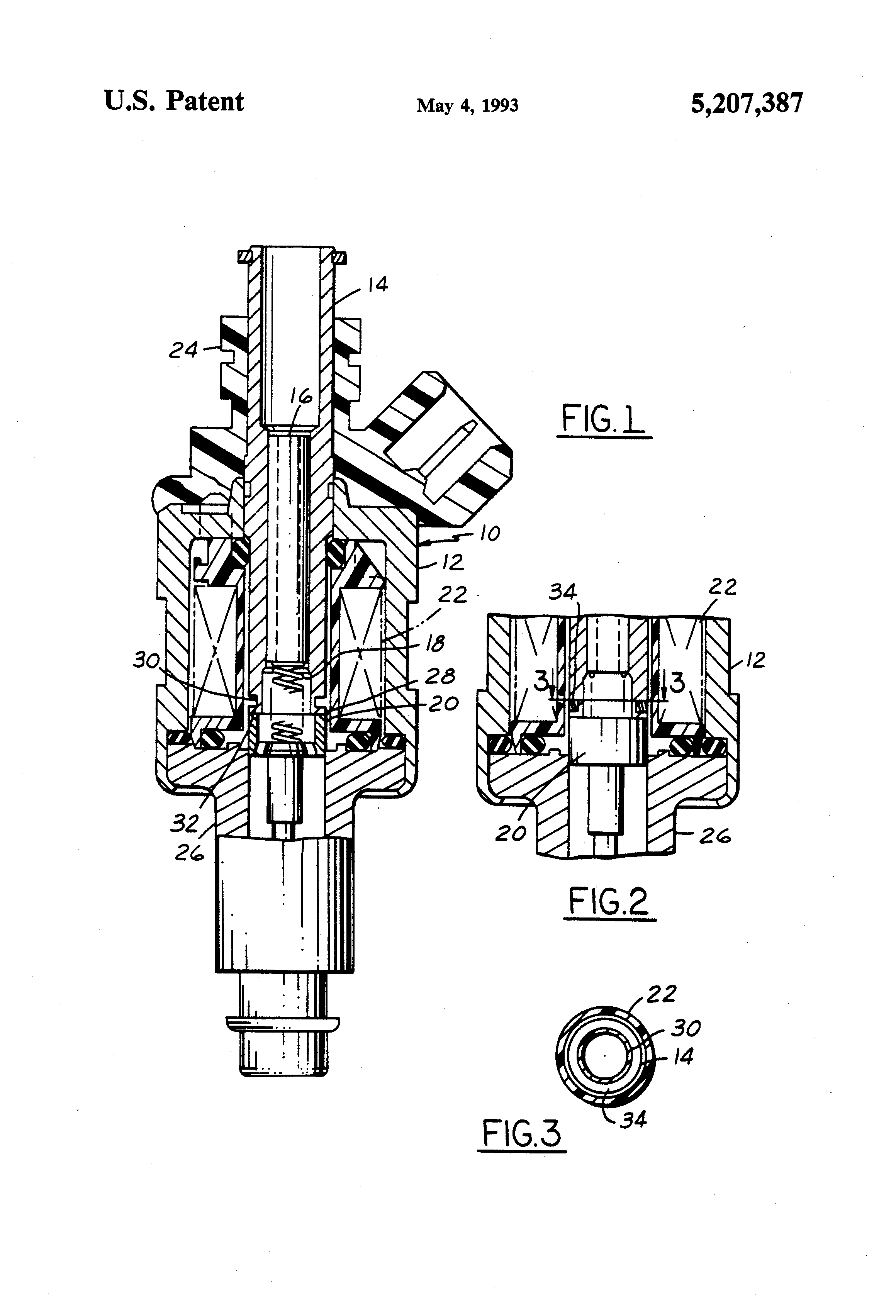
Once it’s past the filter, your gasoline flows into the fuel rail or rails (in the case of most V-shaped blocks) and those feed your injectors, this applies to both direct, multiport, and combined systems. The injectors are solenoids, meaning they are a type of electronic component designed to move in a single direction when they are powered. For most multiport injectors, a coil creates an electromagnetic force that moves the injector needle to its open position. This allows fuel to flow through the pentel of the injector and atomizes the fuel. This atomization allows the fuel to mix with the air and combust with a spark. Fuel as a liquid does not combust easily, but as a mist it combusts easily.
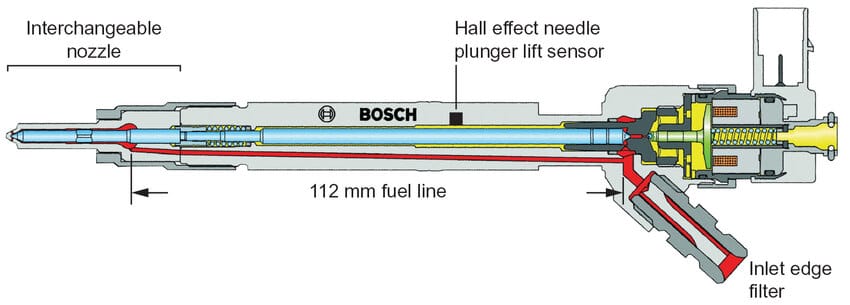
While still a solenoid, the direct injection injector is driven by the piezoelectric effect rather than the electromagnetism of the typical port injector. The piezoelectric effect is more precise and quicker because of electricity causing the internal crystal wafer set—usually made from quartz—to physically expand. It will also not suffer from the effects of electromagnetic saturation that can lead to a hanging injector. This also means the trigger effect is different between them. Reducing the voltage to open the needle rather than increase the on time of the injector’s duty cycle in the case of the electromagnetic injector.
Fuel Pressure Regulator
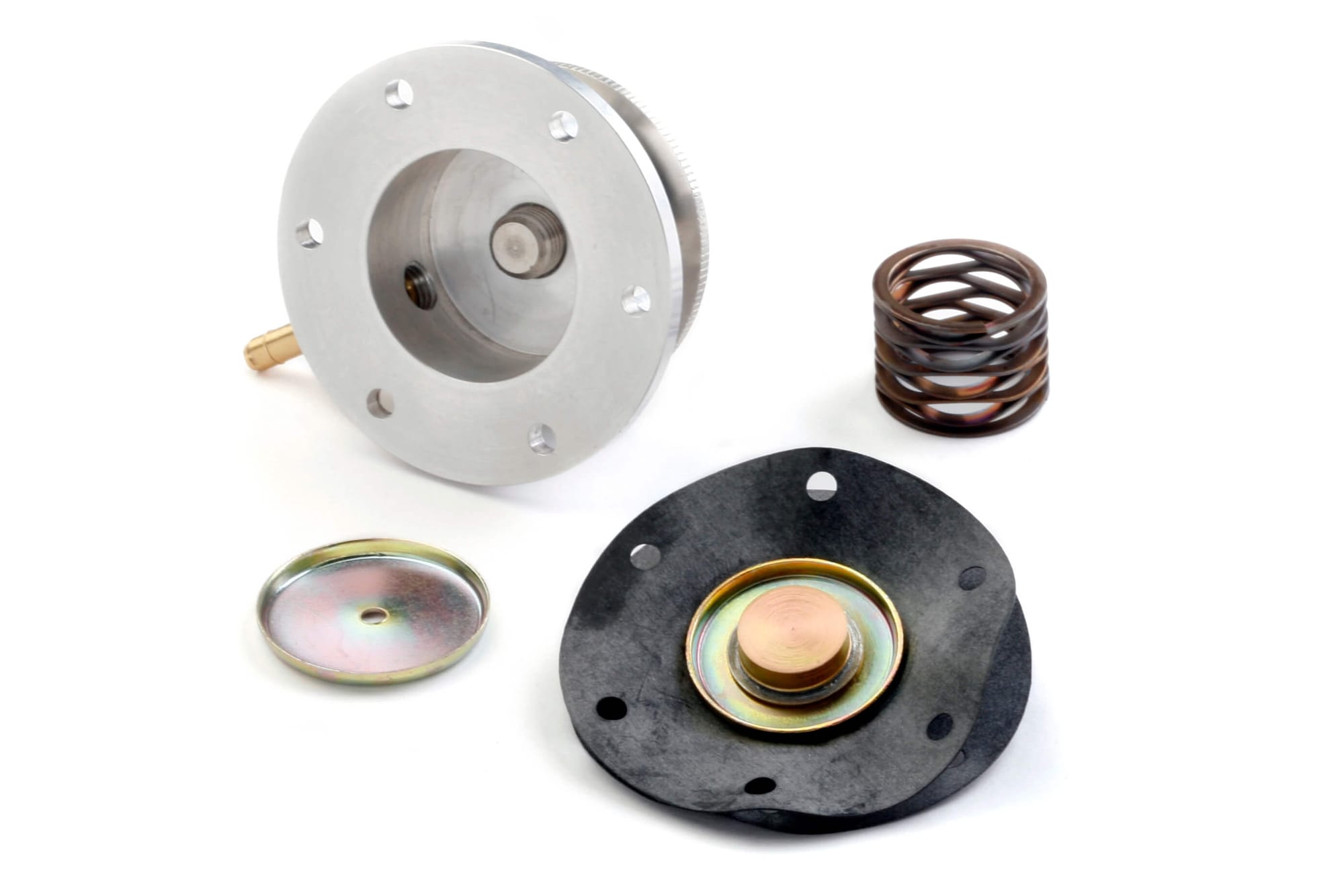
Fuel can’t feel the injectors if there isn’t pressure built into the rails. This pressure is regulated by the aptly named fuel pressure regulator. The most basic regulator is simply a spring with a diaphragm attached to the body of the regulator. When there is enough pressure, the regulator opens and allows fuel to return to the fuel tank via a return line.
However, an engine doesn’t need the same fuel pressure at all loads. Sometimes it needs less when there is a light load, and the fuel injectors are at a very low duty cycle—the rate in which the fuel injectors are open. When you need more fuel, like going up a steep hill, the engine needs more fuel. This means the injectors need to be opened more and will drain the fuel rails much more quickly. That’s why there is a vacuum line on most pressure regulators as engine vacuum will influence how much that diaphragm will open.
High Pressure Pump
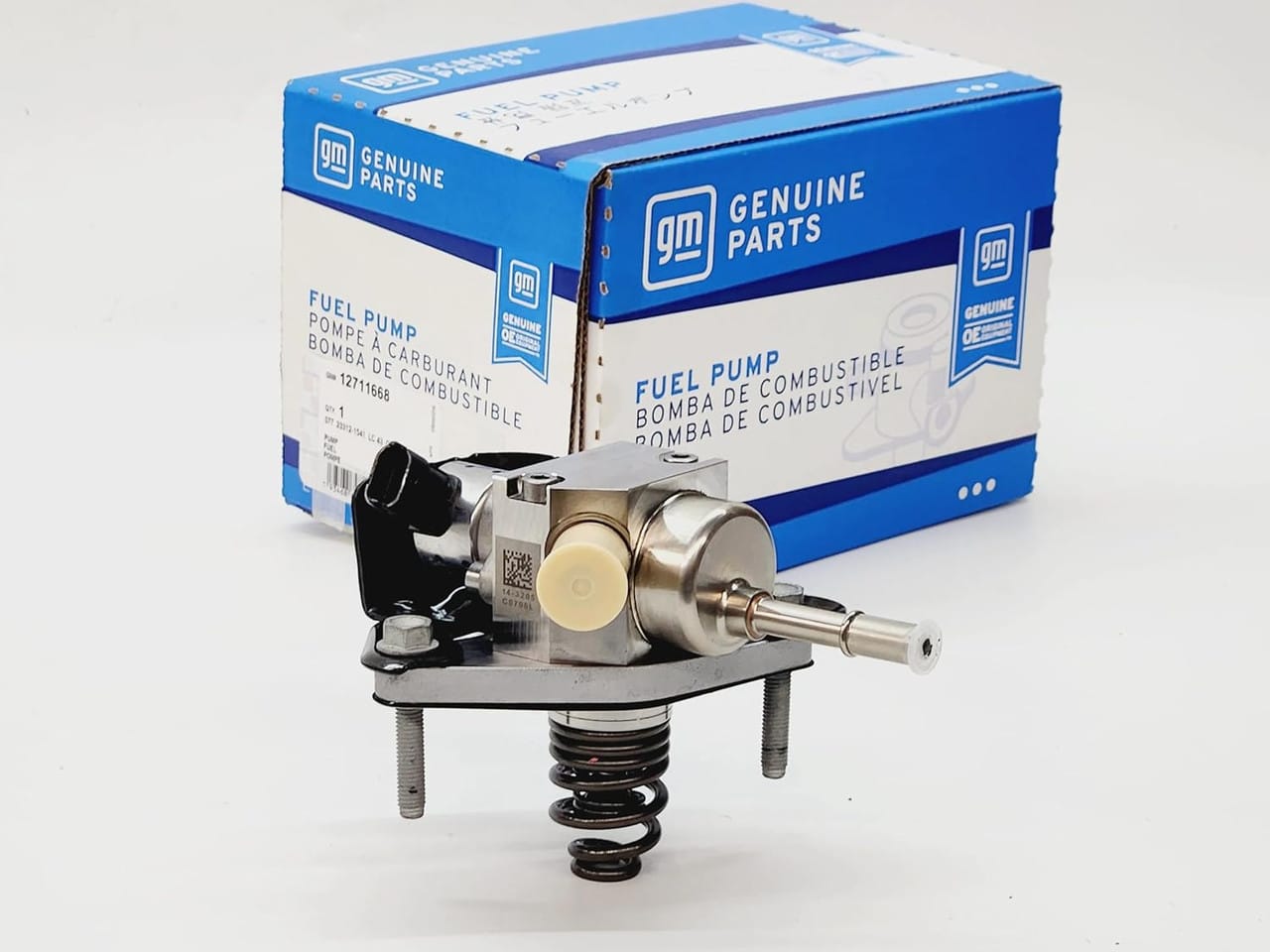
Here again is where the two fuel systems will diverge. The direct injection system requires even higher pressure—up to 29,000 psi versus the 30 to 70 psi of a multiport system—which leads to the need for two pumps and regulators. If you’re familiar with modern diesel engines, you’re probably familiar with this idea as it’s the same with the only difference being the fuel and ignition type.
Initially, the direct injection system is the same as a multiport including the need for a low-pressure regulator and why a dual system can work, it’s just double the parts and why you don’t always find them (despite the valve cleaning advantage). From here, there is a need for away to increase the fuel pressure and that’s done by a secondary fuel pump, usually found close to the fuel rail. The secondary pump will typically be driven off the camshaft of the engine using a special lobe on its camshaft—like old-school carburetor fuel pumps—and raises the pressure from 30 to 70 psi to the staggering 29,000 psi for direct injection. Some manufacturers will drive the pump directly off the camshaft like an old-school distributor, too.
A Return Line, or Not
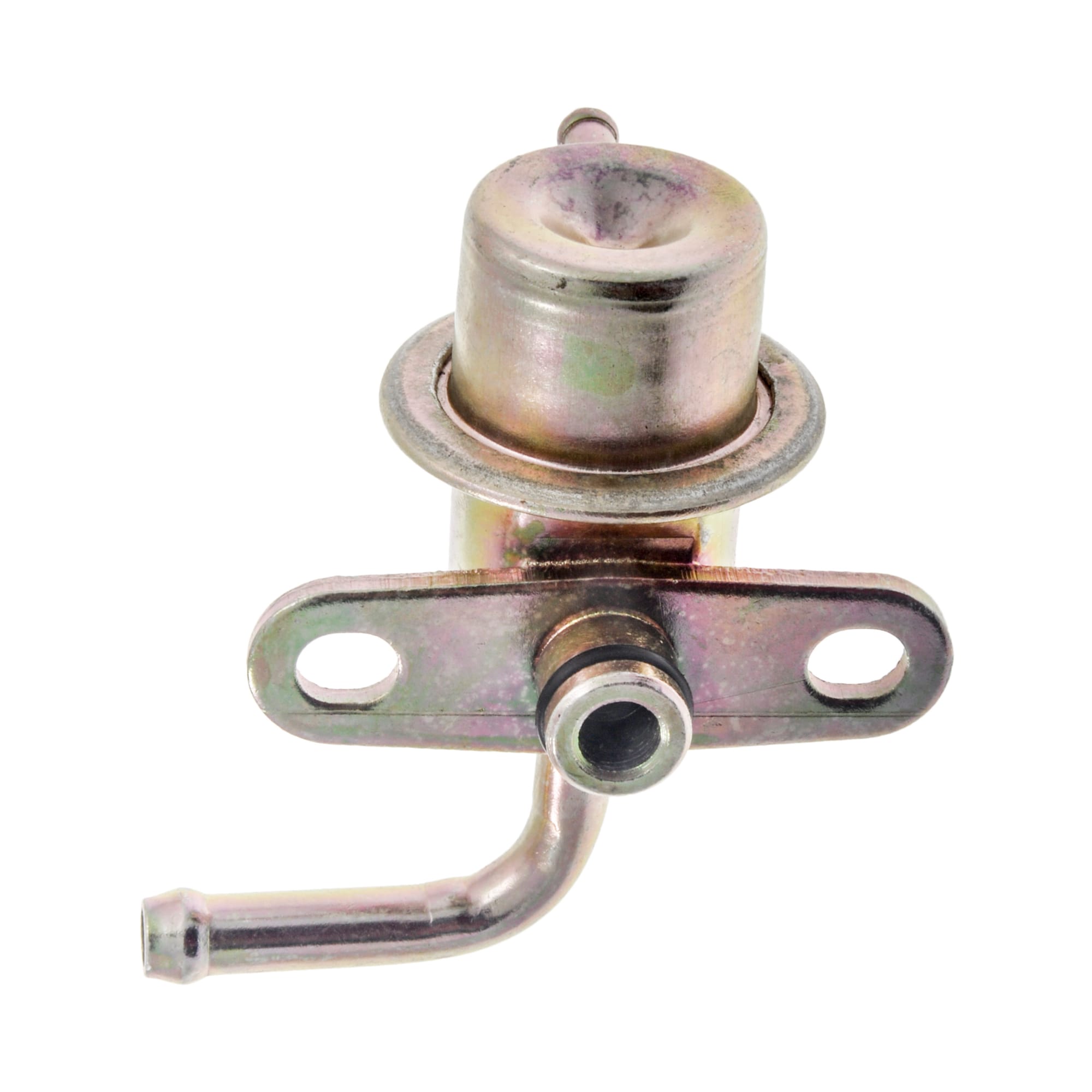
Carburetors that once ruled the automotive world used returnless fuel pressure systems just due to the low supply pressure—less than 20 psi—in these systems. It was only when you needed more pressure to feed larger or multiple carburetors that a return-style fuel pressure regulator became a requirement and usually only found in the automotive performance world. Once multiport injection systems became common place, the fuel pressure regulator required fuel to be fed back into the fuel tank through a fuel pressure return line. This was due to the finite control of the fuel pump by the PCM.
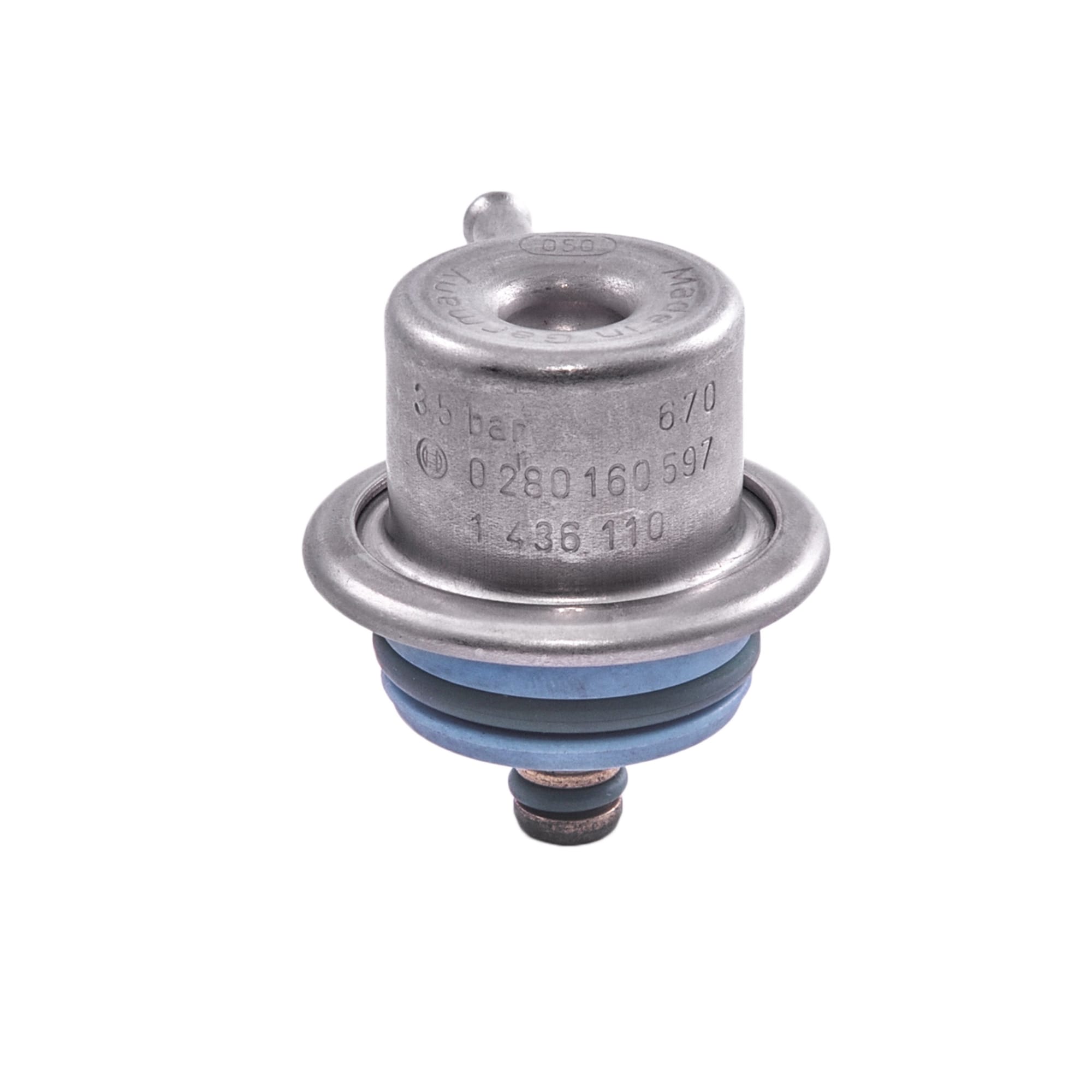
Just before direct injection became common place, a returnless system was reintroduced as control of the fuel pump was now more precise with modern electronic controls like the fuel pump control module (or unit, again, depending on which parts guy you need to talk to). Even with the introduction of direct injection, engine fuel systems remain returnless as pump and regulator control has become even more precise thanks to even tighter regulations on pollution, start-stop technology, and decreasing fuel consumption.
If you like this content and want more, sign up to receive more stories when they go live or support me on Patreon to help me
create more stories and videos like this and more.
Comments ()