Twin Traction Beam Action – A Into TTBs
The Strength of a straight axle, the stability of IFS: This is the Twin Traction Beam Axle
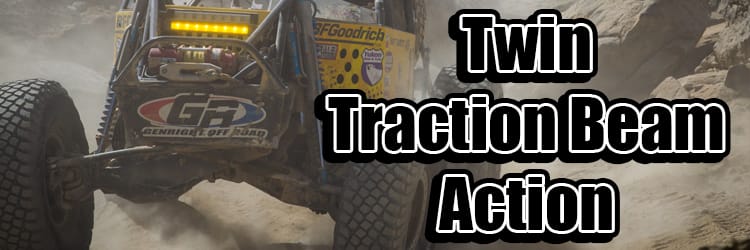
I have taken some interest in the Mistress Racing 4400 rig of Matt Burkett. What makes this unusual from the word go is the fact that it is a Twin Traction Beam front end and for one other reason.
When I first watched Matt take the 4449 up Chocolate Thunder during the Nitto Tire King of the Hammers powered by Optima Batteries, I didn’t quite take in what I was watching. It was only after I started editing the photos that I realized that I witnessed a rarely used Twin Traction Beam four-wheel drive setup.
Before we go any further, I want to encourage you to support me on Patreon. Carbage is going to be hitting it hard this year and I need your help to bring you awesome coverage and content all year long. All you need to do to support Carbage is donate as little as $1 per month. That little amount makes a dramatic difference when more and more people support the site. Now that’s out of the way, let’s get on with the article.
What is Twin Traction Beam?
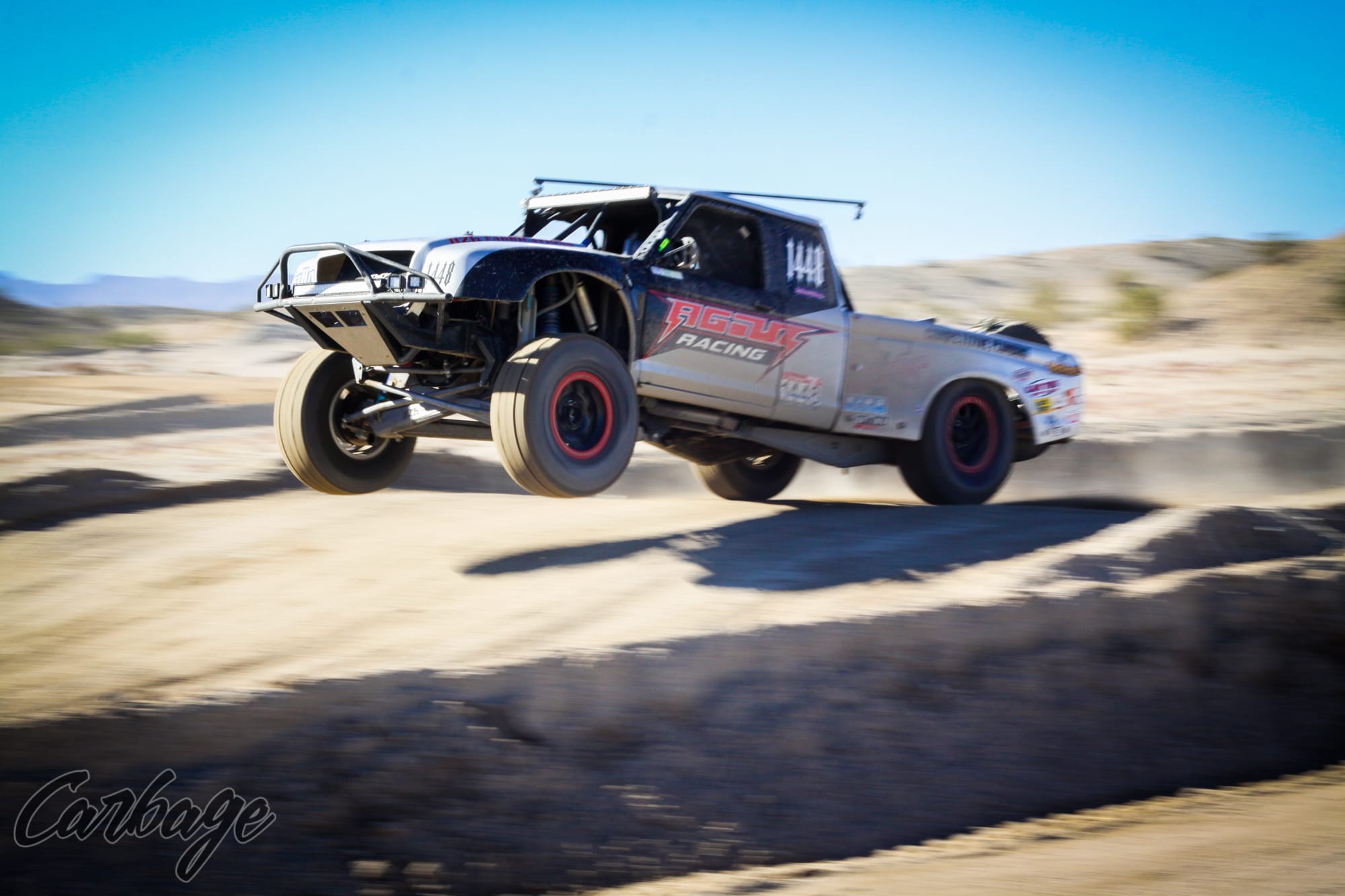
This is a form of swing axle IFS originally made by Ford in 1980. Yes, there is a difference between Twin Traction Beam (TTB) and Twin I Beam made in 1965. The Twin I Beam uses kingpin steering while two-wheel drive (2WD) and four-wheel drive (4WD) TTB designs uses ball joints. There are no Twin I Beam 4WD trucks by definition, either, as solid kingpins make it rather hard to put an axle through them. For 4WD trucks made during the original Twin I Beam era, they were solid front axle designs.
What Makes It Different?
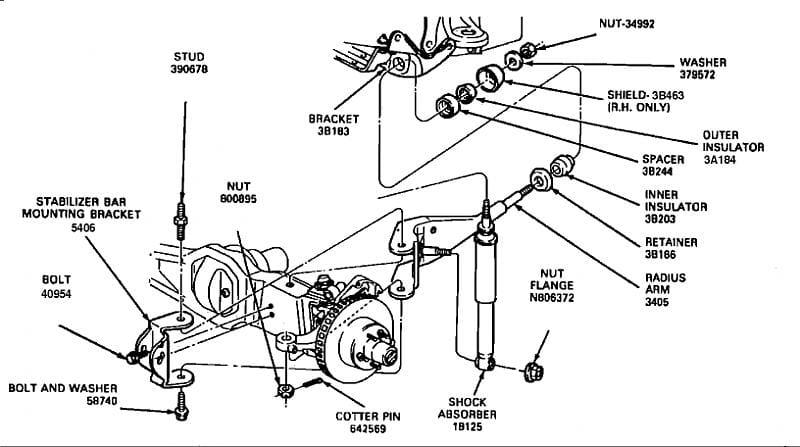
Most of the Ultra4 4400 rigs that use IFS use Short Long Arm (SLA), similar to most modern performance Trucks, Cars, and SUVs use. However, the TTB has an advantage in that it's simpler to use as it's like a straight axle - the pumpkin (where the gears are located) travels with the suspension rather than staying static on the chassis.
This means the front drive axles connected to the wheels don't have to deal with extreme steering angles and suspension angles at the same time. So, you get an independent front end without most of the drivetrain stresses you see in a typical IFS. You also get the high steering angle advantage a straight axle rig does because the axle only has one direction it must bend at the hub.
What Makes It Bad?
However, it does come with some drawbacks. As you can see in the image, the camber changes drastically with wheel travel. In compression, the wheels will camber in (go negative). In droop (the rebound), the wheels will camber out (go positive).
This can make handling interesting as the camber will change as the wheels hit ruts, changes in road camber, rocks, and even changes in steering from suspension travel combined with caster changes. Needless to say, the camber curve is very dynamic. Not as bad as most rear-wheel drive swing axles like you see on bugs (due to the arms being longer on the TTB and Twin I Beam), but still very dynamic.
Steering Arms
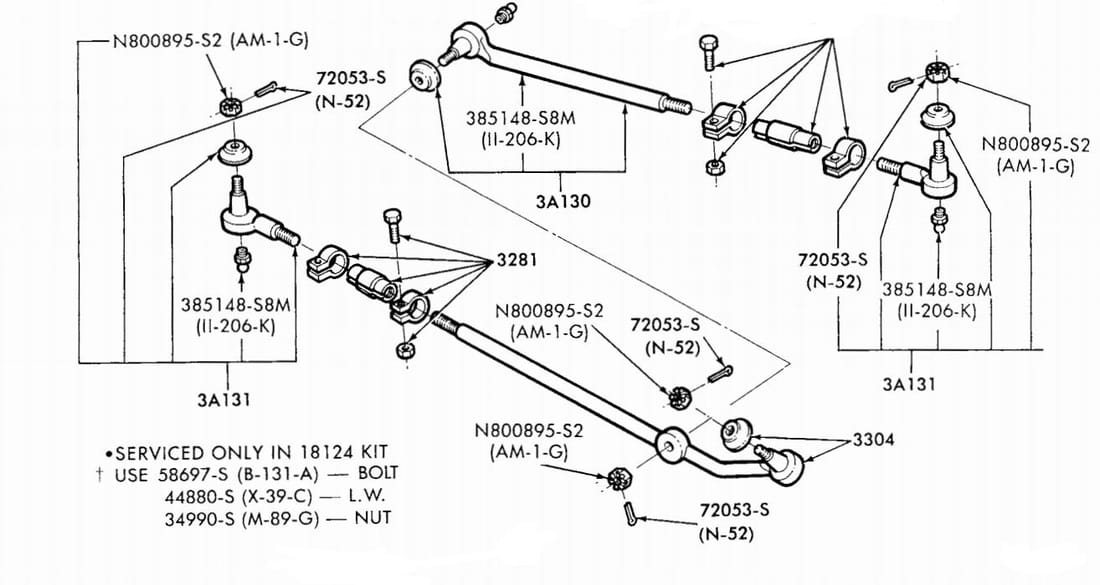
You also must have a very specific steering arm design for TTB. The typical swing-set you see in pitman/idler arm designs don't work because of how travel is done by the entire suspension. Same issue arises if you wanted to use a rack-and-pinion steering. The driver's side axle pivot is attached outboard to the passenger's side of the frame but the passenger's axle pivot is inboard to the driver's side of the frame.
Long Arm, Short Arm, Same Truck
This also means that the beams in the original Ford design are not the same length. The passenger's side axle is almost always shorter. You can make an equal length TTB axle, but it takes a lot of money, engineering, and an even more specific steering linkage design.
Radius Arms
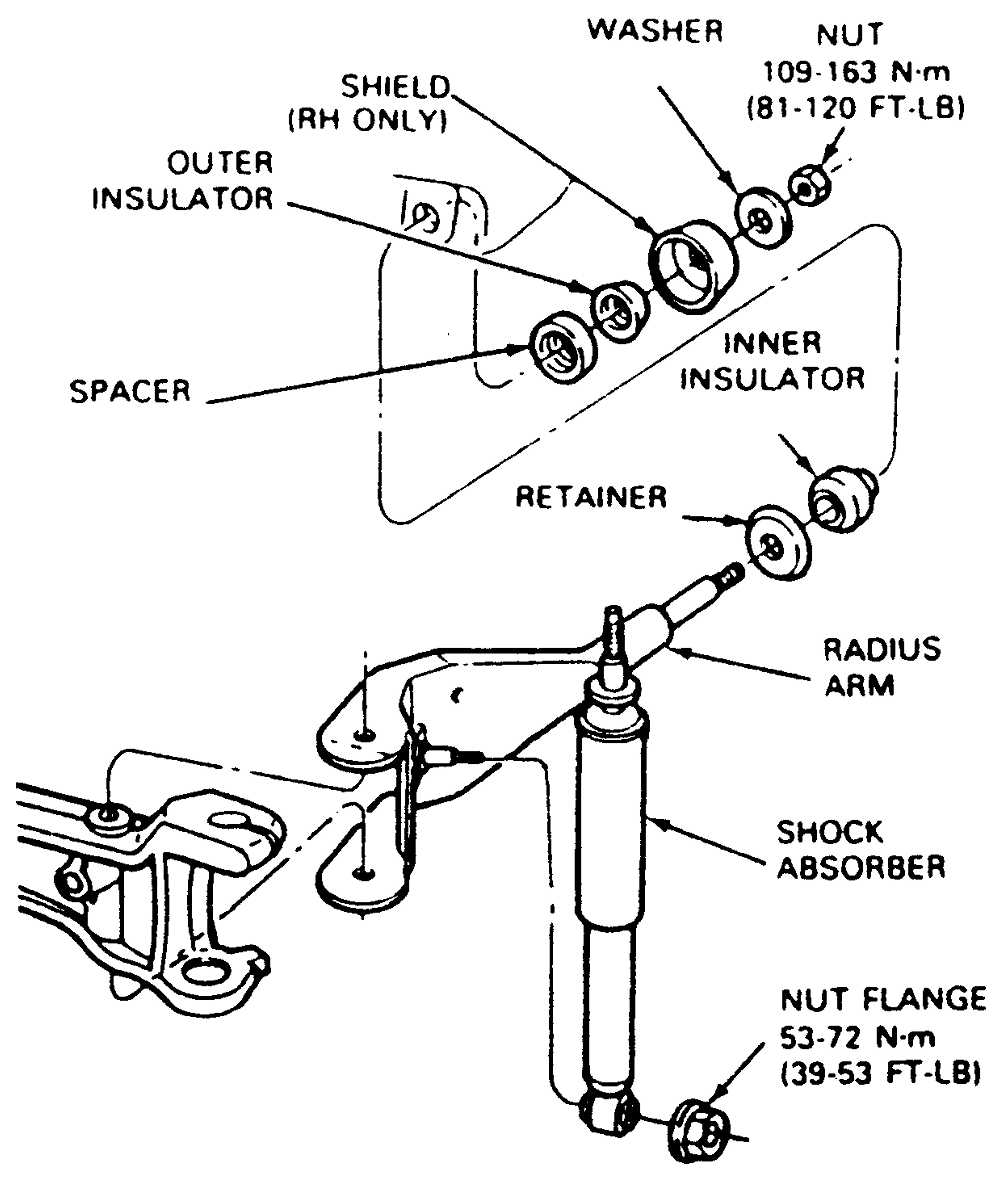
While the design is great for wheel travel, it does introduce a new problem that is usually solved by the linkages of a solid axle suspension: locating the axles forward and aft. This is done by a linkage known as the Radius Arm. This centers the axles as mentioned but also allows them to travel in their arcs. This can be a challenge as the radius arm bushing not only must allow for that twisting motion, but also the forward/aft loading as the wheels hit objects on and holes in the surface.
Advantages
So, with all this in mind, why in the world would anyone use this design? Especially in a professional racing environment? Because there are several advantages over solid axle and SLA suspensions. One is the steering angle. TTB axles are based on Dana straight axle designs.
Dana-Like Features
The knuckles and "inner C's" come from readily available axles like the Dana 35, Dana 44, and Dana 50. You will always find a steering knuckle for these axles in the junkyard and upgrades are very easy to locate. These also use stronger and bigger Universal (UV) Joints that can see more abuse and take the stress of high steering angles since that is the only angle it will see. Constant Velocity (CV) Joints are also becoming a popular upgrade on Dana axles as they continue to gain strength with better metals and casting techniques. Same with the differential carriers, as these are similar to or the same as their Dana straight axle cousins. So, lockers and gears that work on those axles will usually work on the TTBs of the same design.
Strength of A Straight Axle, Handling of A SLA, Kinda
However, you get a better handling rig than you would in a front straight axle version. Each front wheel can take a bump or surface change without disturbing the other. This is an important feature of the TTB/IFS when you're out in the desert sections as handling rules over steering angle and axle toughness. If you can carve your way through the desert faster, you gain an advantage. If you can take the impacts of boulders and can steer around them, you gain an advantage in the rocks. A TTB, on paper, sort of can do both and is why many home-built and some shop-built race trucks continue to utilize it in off-road racing.
If you like this content and want more, sign up to receive more stories when they go live or support me on Patreon to help me create more stories and videos like this and more.
Comments ()